Enhance Your Industrial Processes with Custom Flow Dividers
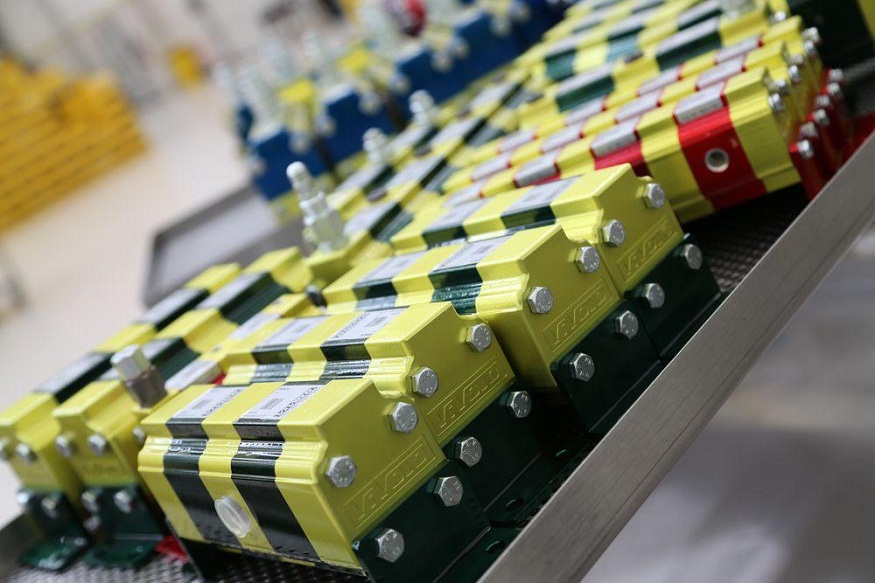
In the world of industrial applications, every detail counts. One of the key components in ensuring optimal performance is the flow divider. These devices play a crucial role in dividing and regulating the flow of fluids in hydraulic systems, ensuring that each part of the system receives the right amount of fluid at the right time. Customizing flow dividers for specific industrial applications can significantly enhance efficiency, reduce costs, and improve system reliability.
In this guide, we will explore best practices in customizing flow dividers, the considerations you need to take into account, and how these components can make a difference in your industrial processes. Whether you’re in manufacturing, oil and gas, or any other industry relying on hydraulic systems, understanding how to tailor flow dividers to your needs is essential.
Understanding Flow Dividers
Flow dividers are hydraulic components used to split the flow of fluid into multiple paths. They ensure that each path receives the exact fluid flow required for optimal operation. This is particularly important in systems where multiple actuators must operate simultaneously and require precise fluid distribution.
In industries like construction, agriculture, and manufacturing, flow dividers are indispensable. They maintain efficiency by preventing fluid wastage and ensure consistent performance across various operations. By customizing flow dividers to fit specific industrial applications, businesses can fine-tune their systems for maximum productivity and reliability.
The Importance of Customizing Flow Dividers
Customizing flow dividers allows industries to address unique operational needs and challenges. Off-the-shelf solutions often fall short in meeting the specific requirements of complex systems. Customization offers a way to tailor flow dividers to handle specific fluid types, pressures, and temperatures, which can vary widely across different industries.
For instance, in the oil and gas sector, equipment must withstand extreme conditions. Custom flow dividers can be designed to handle high-pressure environments and corrosive fluids. Similarly, in the food processing industry, flow dividers must meet stringent hygiene standards while maintaining precise flow control.
By investing in customized solutions, companies can achieve better control over their processes, reduce downtime, and extend the lifespan of their equipment. This tailored approach not only boosts efficiency but also contributes to a more sustainable and cost-effective operation.
Analyzing the Industrial Application Needs
Before customizing flow dividers, it’s essential to have a deep understanding of your industrial application’s needs. Analyzing these requirements involves evaluating the specific demands of your system, such as flow rates, pressure levels, and environmental conditions. This analysis will guide the customization process and ensure that the flow dividers meet your operational expectations.
Key considerations include the type of fluid being used, the temperature range, and the pressure requirements. For example, systems operating in cold environments may require flow dividers with materials that prevent freezing and maintain flexibility. Similarly, systems dealing with abrasive fluids may need dividers made from durable, corrosion-resistant materials.
Understanding these factors is crucial in designing flow dividers that can withstand the rigors of your specific application. It ensures that the dividers are not only effective but also safe and reliable, minimizing the risk of failures and maintenance issues.
Designing for Optimal Performance
The design phase is critical in customizing flow dividers. It involves selecting the right materials, dimensions, and configurations that align with the operational demands of your system. This phase should focus on achieving optimal performance, with considerations for flow accuracy, pressure balance, and energy efficiency.
Precision engineering plays a vital role in this process. The design should allow for seamless integration with existing systems while providing flexibility for future modifications. By working closely with experienced engineers, businesses can develop flow dividers that enhance system performance and deliver long-term value.
Advanced technologies, such as computer-aided design (CAD) and simulation software, can assist in optimizing the design. These tools allow engineers to model different scenarios and test the performance of flow dividers under various conditions. This approach helps identify potential issues early in the design process and ensures that the final product meets all specifications.
Materials Selection for Durability
The choice of materials is a crucial factor in customizing flow dividers. Different industrial applications require specific materials to ensure durability and compatibility with the fluids being handled. The right materials can enhance the lifespan of flow dividers and reduce maintenance costs.
For applications involving corrosive fluids, materials like stainless steel or specialized alloys may be necessary. These materials offer excellent resistance to corrosion and wear, ensuring that the flow dividers maintain their integrity over time. In contrast, applications with high-pressure requirements might benefit from materials with superior tensile strength and impact resistance.
Selecting the appropriate materials involves considering factors such as temperature, pressure, and chemical compatibility. By choosing the right materials, businesses can ensure that their flow dividers deliver reliable performance in any industrial setting.
Ensuring Precision and Efficiency
Precision is paramount in the performance of flow dividers. Accurate flow control ensures that each part of the system receives the correct amount of fluid, preventing overflows and ensuring efficient operation. Customizing flow dividers allows for precise calibration to meet the specific flow requirements of your system.
Efficiency is another critical aspect. Flow dividers should minimize energy consumption and reduce waste. By optimizing the flow paths and ensuring smooth operation, customized dividers can enhance the overall efficiency of your system. This not only reduces operational costs but also contributes to a more sustainable operation.
Advanced technologies, such as flow sensors and control systems, can be integrated into custom flow dividers to enhance precision and efficiency. These technologies provide real-time data on flow rates and pressure, allowing for continuous monitoring and adjustments to optimize performance.
Testing and Quality Assurance
Once the design and customization process is complete, rigorous testing is essential to ensure quality and reliability. Testing should cover all aspects of the flow dividers’ performance, including flow accuracy, pressure handling, and material integrity. This step ensures that the dividers meet all specifications and can withstand the demands of your industrial application.
Quality assurance involves conducting a series of tests under different conditions to verify the performance of the flow dividers. This process helps identify any potential issues and ensures that the dividers are ready for deployment. By working with reputable manufacturers, businesses can ensure that their customized flow dividers meet the highest standards of quality and performance.
Continuous quality assurance is also important. Regular inspections and maintenance checks can help identify wear and tear, ensuring that flow dividers remain in optimal condition. This proactive approach minimizes downtime and extends the lifespan of the dividers.
Cost Considerations
Customizing flow dividers involves an investment, and it’s important to consider the cost implications. While off-the-shelf solutions may seem more economical, they may not deliver the performance and efficiency that customized dividers can offer. Investing in tailored solutions can lead to significant cost savings in the long run.
Customized flow dividers can reduce operational costs by enhancing efficiency and reducing downtime. They can also extend the lifespan of your equipment, minimizing the need for frequent replacements. This long-term cost-effectiveness makes customization a worthwhile investment for businesses looking to optimize their operations.
When considering customization, it’s essential to work with reputable manufacturers who can provide cost-effective solutions without compromising on quality. They can offer guidance on the best materials and designs to meet your budget and operational requirements.
Next Steps
Customizing flow dividers for specific industrial applications offers numerous benefits, from enhanced efficiency to improved reliability. By understanding the unique needs of your operations and working with experienced experts, you can design flow dividers that deliver exceptional performance and value.
For businesses looking to optimize their hydraulic systems, investing in customized flow dividers is a strategic decision. It offers a tailored approach that addresses the challenges and demands of your industry, ensuring that your operations run smoothly and efficiently.