To What Extent Heat Resistant Coating Is Convenient?
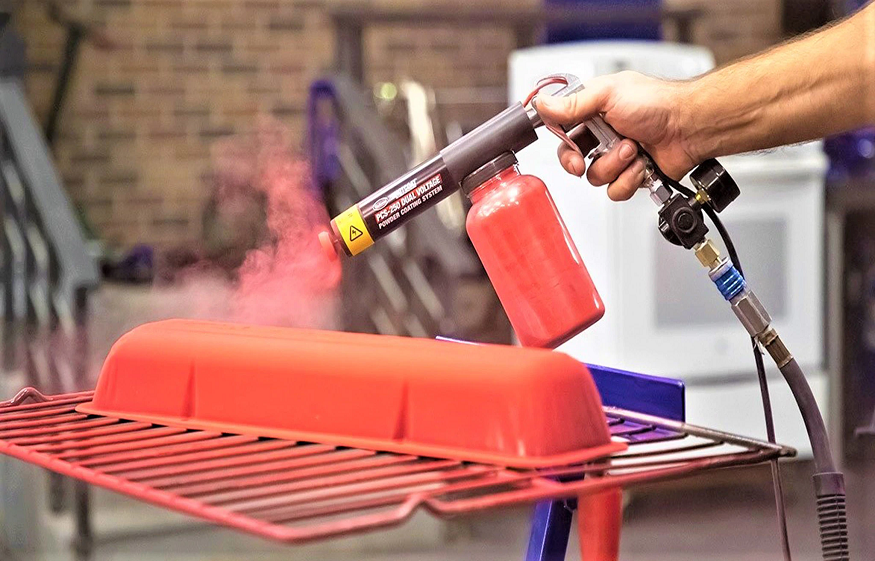
It is possible for a substrate to get damaged by heat and fast temperature swings, which can result in surface fracture and corrosion. Electrical as well as engine components, chimneys as well as ovens, pipes, and chemical facilities are all subjected to temperatures & situations that might be potentially hazardous to their operation. A heat resistant coating (also known as a thermal management coating) is a coating that protects a substrate from temperature changes and extremes without impairing its operation. These coatings, in addition to providing heat protection, also provide:
Corrosion under insulation (CUI) must be protected from corrosion. In between the heated surface as well as the insulation, it adds an additional layer of protection.
Up to 1830°F is the effective temperature range: Temperature resistance varies depending on the formulation, ranging from -320°F to 1830°F in some cases.
Abrasion-resistant: Suitable for use in abrasive conditions.
Reduce thermal fatigue in order to increase the performance of machines and increase the lifespan of individual parts.
Allow for higher working temperatures while keeping heat exposure to a bare minimum.
A coating may be defined as a covering that is attached to the surface of an item, which is referred to as the substrate in most cases. The application of the coating is intended to be both aesthetic and practical or to serve both purposes. The coating itself might be an all-over coating that completely covers the substrate, or it could be a component-specific coating that just covers specific components of the substrate. A food label on several drinks bottles may serve as an illustration of all the coating styles: one component has an all-over purposeful coating (the adhesive), whereas the alternative aspect has one or a number of decorative coatings in such an appropriate sequence (the printing) to establish the pictures and text on the label.
Several industrial coating processes include the application of such a thin film of a specific substance to a substrate such as paper, cloth, film, foil, or sheet stock in order to achieve a specific result. If the substrate is coiled up during a roll and the process begins and finishes on the roll, the method may be referred to as “roll-to-roll” or “web-based” coating. A web is indeed a roll of substrate that has been looped through a coating machine and is commonly referred to as such. Coatings can be applied in a variety of forms, including liquids, gases, and solids.
The evaluation of coatings can be accomplished using a variety of approaches, including both destructive as well as non-destructive techniques. The most often used damaging approach is microscopy of a superimposed cross-section of the coating and substrate, which is the most popular method. Ultrasonic thickness measuring, XRF coatings material thickness, as well as ultra-micro hardness testing are some of the most often used non-destructive procedures.
Paint that is resistant to high temperatures can withstand temperatures of up to 600 degrees Celsius. The coating contains high-heat paint that can withstand temperatures as high as 450 degrees Celsius and as low as 250 degrees Celsius.
Heat-resistant coatings for new construction must meet the following major requirements: excellent performance, more than a wide temperature working range, quick application time, and safe transit from the factory environment to the Jobsite with little handling damage. Many new building installations are covered by the conventional usage of a single size of inorganic zinc (IOZ), or perhaps an inorganic zinc top covered with such a thin film addition of high silicone or an epoxy (heat resistance is normally a maximum of 350°F). Under-insulation applications, on the other hand, are frequently subject to usage limits. It is recommended by NACE SP01-98 that even under insulation, IOZ solutions must only be utilized at temperatures above 120°C (248°F) and that they should not be top-coated with paint. Single-component silicone films are frequently utilized for service beneath insulation because they can withstand a broad range of operating temperatures and provide protection against CUI.
The application of high-temperature liquid paints for maintenance purposes is difficult. Frequently, locations that require maintenance have restricted access or are located in regions that are used by several people. Abrasive blast cleaning is, therefore, frequently not an option, and hand or power tool washing is now the only option for surface preparation. Although many classic coating methods for high-temperature use need surface cleanliness of minimum SSPC-SP 10 “Near-white Blast Cleaning,” the material selection is severely restricted as a result.