Pave The Way For Success Understanding Crack Joint Sealing
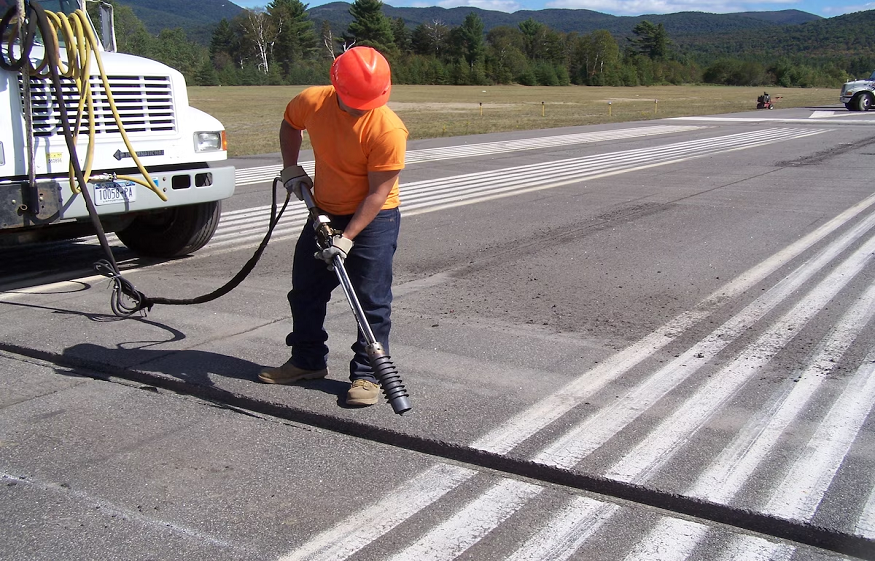
Paving the Way for Success Understanding Crack Joint Sealing
Properly attending to cracks and treating defects promptly delays more costly restoration such as resurfacing or reconstruction. Crack joint sealing is one of the most effective maintenance procedures for pavements.
Sealing prevents incompressible from entering the open joint reservoirs and contributing to spalling upon pavement closure [101]. It also minimizes the passage of surface water.
Sealing a Crack
Before a crack joint sealing, contractors should ensure that the crack or joint is free of debris and moisture. This is often accomplished by power washing, vacuuming, or brushing the cracked surface.
Contractors should also clean the entire length of the joint or crack using a putty knife and margin trowel. Any concrete surface contaminated with a material other than a crack seal will interfere with proper bonding.
When the crack is sealed, it is essential to consider the time of year and regional temperature, as these influence movement in the joint. For example, a compression seal installed in a warm climate will always be in tension and should be designed to accommodate this movement. Surveyors should regularly check the integrity of a crack seal by rating its cohesion loss and the presence of incompressible material [80]. Spalling along a joint is often caused by incompressibility that prohibits expansive movement of adjacent slab sections that generally results in joint closure, and this condition can be reduced by routing and sealing the control joints.
Routing
Crack sealing is a cost-effective preventative maintenance service and, in many cases, is more economical than resurfacing. However, crack joint sealing is only one comprehensive pavement preservation program component.
Routing before applying a rubberized sealant allows the sealant to be more easily stretched into the crack, improving adhesion. It also helps the sealant remain below the surface level, protecting it from traffic and snowplows. Additionally, routing removes dirt and laitance from the existing crack/joint opening and provides a reservoir for the sealant.
The crack/joint must be cleaned thoroughly before applying a rubberized crack sealant. This can be done using compressed air or a heat lance that blows debris away and cleans the cracks/joints. Once the cracks/joints are cleaned, it is recommended that a router such as Crafco’s Model 25 or Model 200 be used to route the existing crack/joint, creating a reservoir for the crack joint sealing material and improving bonding. The routing should be more extensive than the existing crack/joint to ensure proper sidewall adhesion.
Filling a Crack
When repairing isolated cracks in concrete, routing and filling are the most common maintenance procedures. Routed cracks are enlarged and then filled with a sealant or concrete patch material. Filling a crack involves removing all debris and cleaning the surface. Brushing and vacuuming will help keep the new repair from sticking to loose gravel or other items in the crack.
If the crack is intense, it may be necessary to chisel out the sides of the crack for better adhesion of the new material. This will also open up the crack for the movement of water and air that is expected to occur within the structure.
Mix a concrete resurfacing mixture according to detailed product recommendations. Dampen the crack and apply the cement mixture to fill it using a putty knife. Let the mixture dry for an hour, then go over the area with a green float or trowel to make it level with the pavement’s surface.
Sealing a Joint
Joint sealing is a standard maintenance procedure for asphalt and rigid pavements. It prevents water or other non-compressible substances from entering the cracked areas.
Before sealant application, all joints and cracks should be cleaned using the method outlined in the Surface and Preparation section above. Once clean, sandblasting may be required to remove contaminants such as oil, grease, laitance, or dust. Backer rods (such as CERA-ROD from W. R. MEADOWS) can be installed in the joints to control the joint depth and sealant usage. Sealants should be applied according to product specifications and detailed installation instructions.